Digital Twins in Smart Manufacturing
Digital twins manufacturing promises efficiency and innovation in production processes. Discover how this technology can transform your operations.
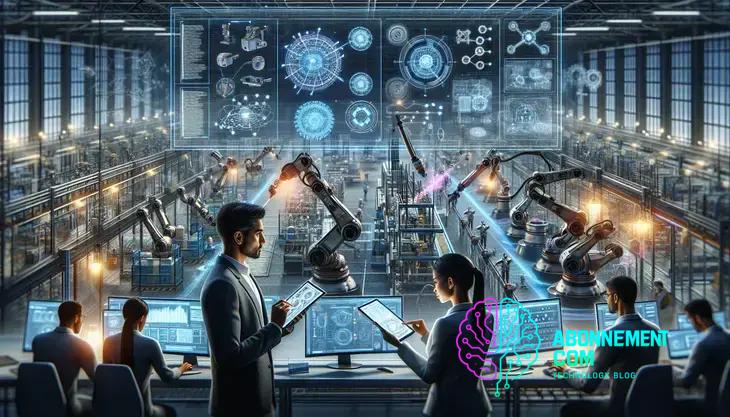
Digital twins in manufacturing represent virtual models of physical systems, using real-time data to optimize processes, enhance efficiency, and enable predictive maintenance, significantly transforming how industries operate.
Digital twins manufacturing is becoming a game-changer in how industries manage their production processes. Have you ever considered how a virtual replica can enhance real-world efficiency? Let’s dive into this innovative approach and explore its potential.
Understanding digital twins in manufacturing
Understanding digital twins in manufacturing is crucial for grasping how technology can streamline operations. A digital twin is a virtual representation of a physical object or system. This technology allows manufacturers to simulate, analyze, and optimize their processes without the risks or costs associated with physical testing.
The Concept of Digital Twins
The concept originated in aerospace and has expanded into various industries, including automotive and healthcare. By integrating real-time data, digital twins provide insights into equipment performance, operational efficiency, and potential failures.
How Digital Twins Work
Digital twins function by collecting data from sensors embedded in the physical object. This data is then processed and fed into a digital model, allowing manufacturers to visualize and interact with their systems. These models can predict outcomes based on different scenarios, facilitating better decision-making.
Benefits of Using Digital Twins
By utilizing digital twins, companies can achieve significant cost savings, improve product quality, and enhance their overall productivity. They enable proactive maintenance, reducing downtime and extending the life of equipment.
Real-World Examples
Many companies have successfully implemented digital twins. For instance, large-scale manufacturers monitor their production lines in real time, identifying inefficiencies and correcting issues proactively. This approach leads to a smarter, more agile manufacturing environment.
The role of data in digital twin technology
The role of data in digital twin technology is vital for creating accurate simulations. Digital twins rely on vast amounts of data collected from sensors on physical assets. This data is continuously analyzed and used to replicate real-world conditions in a virtual environment.
Data Sources
Data can come from various sources, including IoT devices, manufacturing processes, and even user interactions. Each piece of information adds depth to the digital twin, allowing for precise modeling of machinery and systems.
Real-Time Data Processing
One of the significant advantages of digital twins is their ability to process data in real time. This means manufacturers can observe current conditions instantly. With timely updates, companies can make informed decisions, minimizing downtime and enhancing productivity.
Predictive Analytics
Data plays a critical role in predictive analytics within digital twins. By analyzing historical data, manufacturers can forecast future performance and identify potential issues before they arise. This proactive approach not only prevents costly failures but also improves overall efficiency.
Data Integration and Collaboration
Integrating data from multiple sources allows digital twins to provide holistic insights into operations. Collaboration between various departments, such as engineering and maintenance, improves the effectiveness of digital twin applications, resulting in better decision-making and resource management.
Benefits of implementing digital twins
The benefits of implementing digital twins in manufacturing are substantial and can significantly enhance efficiency and productivity. By creating a virtual replica of physical systems, companies can gain valuable insights into their operations.
Cost Savings
Implementing digital twins helps identify inefficiencies and reduce operational costs. By simulating scenarios, manufacturers can optimize processes and avoid wasting resources.
Enhanced Decision-Making
With real-time data and analytics, digital twins improve decision-making processes. Managers can visualize data trends and make informed choices that benefit overall production.
Proactive Maintenance
Digital twins enable predictive maintenance by monitoring equipment conditions in real time. This approach reduces unexpected failures and minimizes downtime, ultimately leading to increased productivity.
Improved Product Quality
By utilizing digital twins, manufacturers can test and refine product designs before physical production. This leads to improved product quality and customer satisfaction.
Faster Time to Market
Implementing digital twins accelerates development cycles. Companies can simulate and iterate designs quickly, reducing the time it takes to bring new products to market.
Challenges faced in adopting digital twins
Adopting digital twins presents several challenges that organizations must navigate. Understanding these obstacles is essential for a successful implementation.
Data Integration Issues
Integrating data from multiple sources can be complicated. Many organizations struggle with incompatible systems and diverse data formats, making it challenging to create a cohesive digital twin.
High Initial Costs
The initial investment for developing digital twins can be significant. Companies must consider costs related to software, hardware, and personnel training, which can deter some organizations from adoption.
Skill Gaps and Training Needs
To effectively utilize digital twins, companies often find that their workforce lacks the necessary skills. Training employees and hiring new talent can add to the challenges, requiring time and financial resources.
Change Management Resistance
Some employees may resist changes associated with adopting digital twin technology. Overcoming this cultural resistance is critical for successful integration and requires effective communication and change management strategies.
Data Security Concerns
With increased connectivity and data sharing, organizations must address security concerns. Protecting sensitive information becomes more challenging as the digital twin relies on real-time data from various sources.
Real-world applications of digital twins
Real-world applications of digital twins are transforming various industries by providing innovative solutions and enhancing operational efficiency. These applications illustrate how companies utilize digital twin technology to optimize their processes.
Aerospace Engineering
In aerospace, digital twins are used to simulate aircraft performance under different conditions. This helps engineers predict maintenance needs and improve safety by analyzing potential issues before they arise.
Manufacturing
Manufacturers employ digital twins to create virtual models of production lines. By analyzing these models, they can identify bottlenecks, reduce waste, and enhance production efficiency without interrupting actual operations.
Healthcare
In healthcare, digital twins enable the simulation of patient treatments and outcomes. Doctors can predict how a patient will respond to a particular treatment, thereby personalizing healthcare and improving patient outcomes.
Smart Cities
Digital twins are essential in developing smart cities. They allow urban planners to simulate city operations, such as traffic flow and resource management, leading to more efficient urban environments.
Energy Management
Utility companies utilize digital twins for energy management. By simulating power plants and distribution networks, they can optimize energy production and distribution, ultimately lowering costs and improving service reliability.
Integrating digital twins with IoT and AI
Integrating digital twins with the Internet of Things (IoT) and Artificial Intelligence (AI) creates powerful synergies that enhance operational efficiency and innovation. This integration allows businesses to leverage real-time data and advanced analytics.
Real-Time Monitoring
When digital twins are connected to IoT devices, they can receive continuous updates from physical assets. This real-time monitoring helps organizations track performance, identify anomalies, and respond quickly to issues.
Enhanced Predictive Analysis
The combination of digital twins and AI enables sophisticated predictive analysis. By analyzing data captured from IoT devices, AI models can forecast potential failures and recommend preventive actions, ensuring reliability and minimizing downtime.
Optimized Resource Management
Integrating these technologies allows companies to optimize resource use. Digital twins provide insights into how resources are utilized, and IoT devices collect data on supply levels, helping organizations manage inventory more effectively.
Improved Decision-Making
The insights drawn from AI-driven digital twins enhance decision-making processes. Companies are better equipped to make informed choices regarding operations, maintenance, and production strategies based on data-driven insights.
Scalability and Flexibility
This integration fosters scalability and flexibility. As businesses grow, digital twins can easily adapt to new inputs from additional IoT devices, allowing for the expansion of monitoring capabilities without significant disruptions.
Future trends in digital twins manufacturing
The future trends in digital twins manufacturing show exciting possibilities that can reshape the industry. As technology evolves, manufacturers are finding new ways to enhance productivity and streamline operations.
Increased Use of AI and Machine Learning
AI and machine learning will play a larger role in digital twins. These technologies will enhance predictive analytics, allowing manufacturers to optimize processes based on real-time data and historical patterns.
IoT Integration
The integration of IoT devices will continue to grow, providing digital twins with more accurate and timely data. This connectivity will allow for real-time monitoring of equipment and processes, improving response times and efficiency.
Lifecycle Management
Future digital twins will focus more on lifecycle management. Manufacturers will use digital twins not just for production but also for ongoing maintenance and life prediction of assets, ensuring lower operational costs and extended lifespans.
Customization and Personalization
As personalization becomes a priority, digital twins will enable customized manufacturing solutions. Companies can model individual customer preferences, leading to tailored products and enhanced customer satisfaction.
Sustainability Efforts
Digital twins will contribute to sustainability initiatives by helping manufacturers assess the environmental impact of their operations. By simulating different scenarios, companies can identify areas to reduce waste and improve energy efficiency.
Case studies showcasing successful implementations
Case studies showcasing successful implementations of digital twins provide valuable insights into how this technology can transform operations across various industries. These examples highlight the practical benefits and innovative solutions that organizations have achieved.
Aerospace Industry Example
One leading aerospace company adopted digital twins to simulate aircraft systems. By using real-time data from sensors, they improved predictive maintenance. This reduced downtime during operations significantly and enhanced safety protocols.
Automotive Manufacturing Case
An automotive manufacturer implemented digital twins to model the entire production line. This allowed them to identify bottlenecks in the assembly process. With these insights, they optimized operations and increased production speed by 15% while maintaining quality standards.
Healthcare Success Story
A healthcare provider utilized digital twins to create virtual models of surgical procedures. By simulating surgeries, doctors could plan operations more effectively, reducing the risk of complications. This led to improved patient outcomes and faster recovery times.
Smart City Initiative
A city planning department used digital twins to optimize traffic management. The simulation of traffic patterns helped in redesigning road layouts, which decreased congestion by 30%. This initiative increased overall efficiency in urban transport.
Energy Sector Implementation
A power company deployed digital twins to monitor and manage energy grids. By analyzing performance data, they identified inefficiencies in power distribution. This improvement resulted in a 20% reduction in energy loss, contributing to sustainability goals.
Best practices for developing digital twin strategies
Implementing digital twin strategies effectively requires careful planning and adherence to best practices. Here are key strategies that organizations can follow to maximize the benefits of digital twins.
Define Clear Objectives
Before starting, it is essential to define clear objectives for what you want to achieve with digital twins. Setting specific goals helps guide the implementation process and measure success.
Invest in Quality Data
Digital twins rely on accurate and timely data. Investing in quality data collection mechanisms, such as IoT sensors and monitoring systems, ensures that the digital twin reflects real-world conditions.
Ensure Cross-Departmental Collaboration
Collaboration among different departments is crucial. Involving teams from engineering, IT, and operations ensures that the digital twin is comprehensive and addresses various perspectives within the organization.
Focus on Scalability
Build your digital twin strategy with scalability in mind. As your business grows, the digital twin should easily adapt to include new assets and data sources without major disruptions.
Continuous Improvement
Digital twin technologies are evolving rapidly. Organizations should prioritize continuous learning and improvement. Regularly update the digital twin based on feedback and changing operational requirements.
Training and Development
To maximize the effectiveness of digital twins, investing in training for staff is essential. Ensure that employees understand how to use the technology and interpret the insights generated by digital twins.
In conclusion, the future of digital twins in manufacturing
The use of digital twins is transforming how industries operate, offering significant benefits such as improved efficiency, predictive maintenance, and better resource management.
By integrating digital twins with technologies like AI and IoT, businesses can gain real-time insights that enhance decision-making and streamline operations.
However, developing effective digital twin strategies requires careful planning, collaboration across departments, and ongoing investment in quality data and training.
As companies continue to embrace this technology, the potential for innovation and growth will only increase. Therefore, it’s essential for organizations to stay informed and adapt to the evolving landscape of digital twin technologies.