3D Printing Electronics: The Next Revolution
3D printed electronics are changing the way we design and create gadgets. Discover how this technology impacts your daily experiences and future innovations.
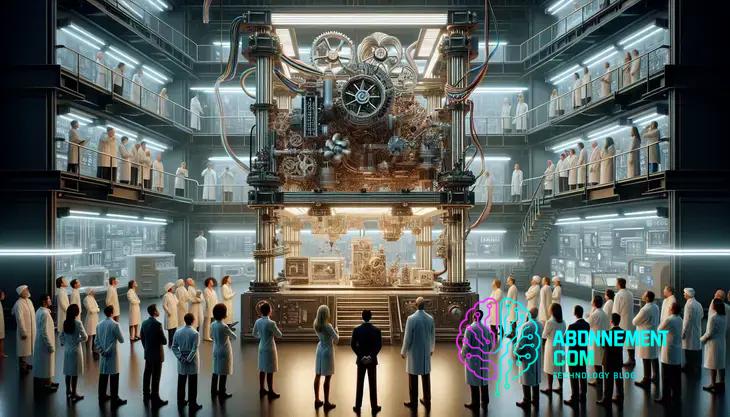
3D printed electronics enable the creation of complex, customized electronic components quickly and cost-effectively, offering significant advantages in industries like healthcare, aerospace, and consumer electronics.
3D printed electronics are transforming the way we think about technology and design. Have you ever considered how these innovations might simplify or enhance your daily gadgets? Join me as we explore this fascinating realm.
Understanding 3D printed electronics
Understanding 3D printed electronics involves exploring how this innovative technology merges traditional 3D printing with electronic components. This process enables the creation of complex, functional devices that combine mechanical and electronic features into a single product.
3D printed electronics can produce various components like circuit boards, sensors, and even batteries. The ability to print these elements together leads to a significant reduction in production time and cost, providing unprecedented flexibility in design.
Moreover, this technology allows for rapid prototyping, which is essential in today’s fast-paced tech world. Engineers can quickly iterate designs, test various models, and refine components more efficiently than traditional methods allow.
By using materials that are specifically designed for electronic applications, such as conductive inks and flexible substrates, manufacturers can create lightweight and compact devices that were previously impossible to produce. This aspect of 3D printed electronics opens the door to new applications in wearables, IoT devices, and innovative consumer electronics.
As industries continue to explore the potential of 3D printed electronics, we can expect to see significant advancements in the way we design and interact with our gadgets, potentially changing the landscape of consumer electronics entirely.
The technology behind 3D printed electronics
The technology behind 3D printed electronics combines advanced printing techniques with electronic component design. At the heart of this process is additive manufacturing, where materials are layered to create objects, as opposed to traditional subtractive methods.
Conductive materials play a crucial role in 3D printed electronics. These materials, which can include conductive inks and filaments, allow for the creation of electrical pathways within the printed objects. This enables the integration of circuits directly into the design, streamlining production.
One popular technology is inkjet printing, where circuits are printed using a precise application of conductive ink. This method allows for fine detail and complex circuit designs, making it suitable for intricate electronic components.
Stereolithography (SLA) is another method used in this field. SLA utilizes a laser to cure liquid resin into solid layers. When combined with conductive materials, SLA can produce high-resolution electronic parts, offering both excellent detail and functionality.
The development of smart materials, which can change properties in response to external stimuli, is another exciting area within 3D printed electronics. These materials can enable the creation of devices that interact with their environment, making them useful in applications like sensors.
Furthermore, flexible electronics are gaining traction in the 3D printing domain, allowing devices to be lightweight, bendable, and adaptable to various surfaces. This flexibility opens new possibilities for wearables and other consumer electronics.
Applications of 3D printed electronics in industries
Applications of 3D printed electronics in industries are vast and varied, showcasing the versatility of this technology across multiple sectors. One of the most significant areas is in consumer electronics, where manufacturers create complex circuit boards and components that are lighter and more efficient.
In the healthcare sector, 3D printed electronics enable the development of custom medical devices. For instance, prosthetics and implants can be tailored to fit individual patients perfectly. Additionally, wearable health devices can integrate smart sensors directly, offering real-time data collection for better patient monitoring.
Aerospace also benefits from this technology. Engineers use 3D printed electronics to produce lightweight components that help improve fuel efficiency. These parts can be customized for optimal performance, which is critical in aviation.
Moreover, the automotive industry is making strides with 3D printed electronics by integrating them into smart vehicles. This includes advanced driver-assistance systems (ADAS), which rely on sensors and electronics printed into complex geometries, allowing for space-saving designs and improved functionality.
In the field of IoT (Internet of Things), 3D printed electronics enable the creation of smart devices that can communicate with one another seamlessly. These devices often require complex sensor arrangements that are efficiently created using 3D printing techniques.
Finally, the educational sector is using 3D printed electronics to provide hands-on learning experiences. Students can design and print their own prototypes, gaining skills in both electronics and engineering.
Benefits of using 3D printed electronics
Benefits of using 3D printed electronics are numerous and transformative for various industries. One significant advantage is cost-effectiveness. 3D printing reduces material waste and allows for shorter production runs, making it easier for companies to produce small batches of custom components without incurring high costs.
Speed is another benefit. The rapid prototyping enabled by 3D printed electronics allows designers to quickly test and iterate on their ideas. This can significantly shorten the product development cycle and bring innovations to market faster.
Moreover, customization is a key feature. With 3D printing, manufacturers can easily modify designs to meet specific customer needs. This flexibility leads to products that are better suited for their intended applications, enhancing user satisfaction.
Reduced assembly time is also a crucial benefit. By integrating multiple electronic components into a single printed object, fewer parts need to be assembled manually. This simplification speeds up production and minimizes the chances of assembly errors.
The ability to create complex geometries is another major advantage. 3D printing can produce intricate designs that would be impossible or prohibitively expensive to create using traditional manufacturing methods. This opens new possibilities for innovation in product design.
Lastly, environmental sustainability is a growing concern. 3D printing often uses less energy and generates less waste compared to traditional manufacturing processes. As industries seek to become more eco-friendly, the adoption of 3D printed electronics can contribute to these sustainability goals.
Challenges faced in 3D printing electronics
Challenges faced in 3D printing electronics are significant and can impact the success of this technology in various industries. One of the primary challenges is material limitations. While 3D printing offers a range of materials, not all are suitable for electronics. Finding conductive materials that work well with 3D printing processes can be difficult.
An additional challenge is precision and resolution. Achieving the highly detailed and precise components required for electronic devices can be challenging with some 3D printing technologies. Manufacturers must ensure that printed components meet strict tolerance requirements.
Integration with traditional manufacturing processes poses another hurdle. Many companies are still reliant on conventional production methods, making it challenging to fully adopt 3D printed electronics. Transitioning to this new technology requires adjustments to existing workflows and training of personnel.
Another issue is regulatory compliance. Electronic devices must adhere to various safety and performance standards. Ensuring that 3D printed electronics meet these regulations can complicate the design and production process.
Additionally, quality control is a concern. Ensuring consistency and reliability in printed components is critical, as any defect can lead to product failure. Manufacturers need to establish strict testing protocols to maintain high standards.
Lastly, high initial investment costs for 3D printing technology can deter businesses from making the switch. This technology can require expensive equipment and training, which may be a barrier for smaller companies looking to enter the market.
Future trends in 3D printed electronics
Future trends in 3D printed electronics promise to change the landscape of manufacturing and technology significantly. One major trend is the integration of AI and machine learning into the design and production processes. These technologies can analyze data to optimize designs, predict failures, and streamline manufacturing, enhancing the efficiency of 3D printed electronics.
Another trend is the use of advanced materials. Research is ongoing into developing new materials that offer better conductivity, flexibility, and durability. For instance, materials that can withstand extreme conditions or that have self-healing properties could revolutionize various applications.
Personalization is expected to grow as more industries embrace 3D printing. As consumers demand customized products, manufacturers will look to design unique electronic components tailored to individual needs. This shift could lead to more innovative products in sectors like wearable technology and smart home devices.
The push for sustainability is influencing future developments as well. Companies are focusing on reducing waste and using eco-friendly materials in 3D printing processes. This trend aligns with global priorities towards greener practices.
Collaboration between industries will likely increase, as sectors such as healthcare, automotive, and aerospace explore the benefits of 3D printed electronics. Sharing knowledge and resources can lead to breakthroughs in product innovation and performance.
Lastly, the emergence of cloud-based 3D printing services may make this technology more accessible. As more companies offer on-demand printing services, businesses will have the flexibility to create parts as needed without significant upfront investment in equipment.
Comparison with traditional electronics manufacturing
Comparison with traditional electronics manufacturing reveals significant differences that impact production efficiency and product design. Traditional electronics manufacturing often relies on subtractive methods, where materials are cut away to create components. In contrast, 3D printed electronics use additive manufacturing, layering materials to build components from the ground up.
One major advantage of 3D printing is reduced waste. Since it adds material only where needed, there is significantly less scrap compared to traditional methods. This not only saves costs but also contributes to more sustainable manufacturing practices.
Another key area is design flexibility. Traditional manufacturing often restricts design due to tooling limitations. However, 3D printing allows for complex geometries and customized designs that would be challenging or impossible to create using conventional means.
Production speed is also a critical factor. 3D printing can drastically reduce the time it takes to move from design to finished product. With traditional manufacturing, creating molds or tooling can be time-consuming. 3D printing eliminates many of these steps, enabling quicker iterations and faster market entry.
On the other hand, traditional manufacturing techniques may offer better scalability for mass production. Once a design is finalized, producing large quantities with conventional methods can be more efficient than printing each part individually, which might slow down production.
Moreover, regulatory compliance can vary between the two methods. Traditional electronics have established processes and standards that must be adhered to, which can make certification easier. In contrast, 3D printed electronics may face unique challenges in meeting these standards due to new materials and processes.
How to start with 3D printed electronics
How to start with 3D printed electronics involves a few essential steps to ensure a smooth and effective introduction to this innovative technology. First, it is crucial to identify your goals. Determine what you want to achieve with 3D printed electronics, whether it’s prototyping, custom components, or production of final products.
Next, invest in the right equipment. Choose a 3D printer that suits your specific needs. Consider features like build size, printing speed, and the types of materials it can use. Additionally, make sure the printer supports electronic components if that is part of your plan.
After acquiring the printer, select proper materials. Finding the right conductive inks or filaments is vital for your projects. Look for materials that are compatible with your printer and suited for electronics applications.
Familiarize yourself with design software. Software tools are essential for creating the electronic designs you want to print. Programs like CAD (Computer-Aided Design) can help you design intricate components and layouts tailored to your needs.
Once you have the designs ready, test your prototypes. Start with simple projects to understand the printing process and how to optimize designs for better results. This approach will help you learn about the capabilities and limitations of your equipment.
Finally, continuously improve your skills. Staying updated on trends, techniques, and materials in 3D printed electronics will enhance your capabilities and open up new avenues for innovative projects.
Real-world examples of 3D printed electronics
Real-world examples of 3D printed electronics showcase the significant impact of this technology across various industries. In the healthcare sector, companies are using 3D printed electronics to create custom prosthetics and implants. These devices are tailored to fit individual patients perfectly, improving comfort and effectiveness.
Another example can be found in consumer electronics. Various startups and established companies have begun using 3D printing to develop lightweight headphones and wearables. This innovation allows for complex designs that enhance both functionality and aesthetics.
The aerospace industry is also benefiting from 3D printed electronics. Manufacturers are producing lightweight, high-performance components for aircraft. These parts can reduce overall weight, leading to improved fuel efficiency and lower emissions.
In the field of automotive technology, companies are utilizing 3D printing for creating smart dashboards with embedded electronics. These integrated solutions simplify installation and reduce the number of individual components needed.
Educational institutions are adopting 3D printed electronics as well. Schools and universities use this technology to teach students about electronics and engineering. Projects involving 3D printed sensors and devices foster creativity and hands-on learning.
Companies are also experimenting with smart home devices that integrate 3D printed components. These devices can include custom designs for lighting, alarms, or even IoT products, allowing users to personalize their home automation systems.
In conclusion, the future of 3D printed electronics is bright
3D printed electronics are changing the way we design and manufacture products across various industries. From healthcare to consumer electronics, the benefits are clear.
This technology offers customization, faster production, and significant cost savings. As more companies embrace 3D printing, we can expect even more innovative solutions to emerge.
While challenges remain, the potential of 3D printed electronics to enhance functionality and creativity is enormous. By understanding the advantages and starting to implement this technology, businesses and individuals can remain competitive in a rapidly evolving market.
Overall, the possibilities with 3D printed electronics are endless, and now is the time to explore them.